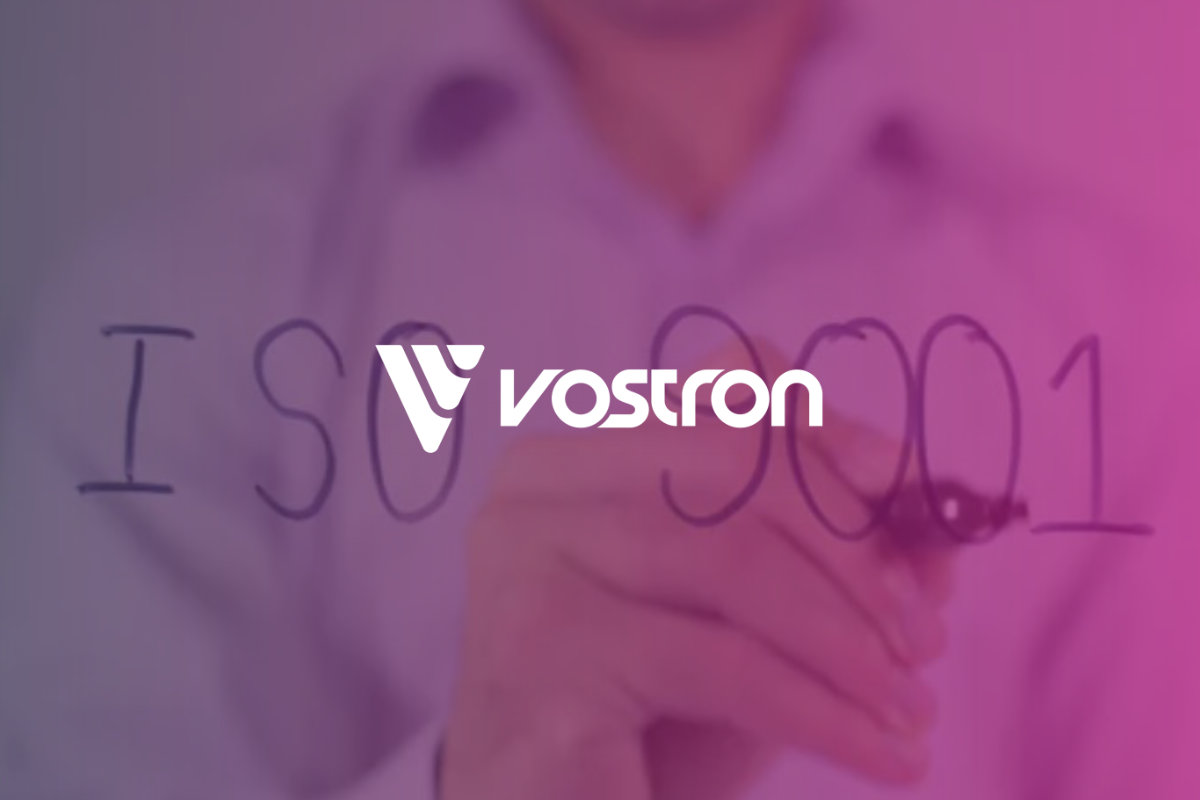
15 May ISO 9001 Explained
ISO 9001 is the internationally recognised standard for Quality Management. Used by over 1 million companies; it was created to give organisations the tools they need to gain more business, reduce costs, and improve productivity. ISO 9001 certification also provides customers with confidence that they will receive reliable, quality products and services. ISO 9001 is perfect for any organisation, large or small, looking to improve quality and consistently meet customer requirements.
ISO 9001 is known to have benefits such as: increased efficiency, international recognition, greater employee satisfaction and morale and improved customer gratification.
In this article we will be discussing some of the key factors of ISO 9001 that are important to understand and take into account.
Process Approach
ISO 9001 is based on a process approach, which means that an organization’s activities and processes are viewed as interconnected and part of a larger system. This approach encourages organizations to identify and manage their processes in a more systematic way, which can lead to greater efficiency, consistency, and customer satisfaction. They do in several steps:
- Identifying processes – The first step in the process approach is to identify the key processes that are involved in delivering products or services to customers. This may involve mapping out the various stages of production, delivery, and support.
- Defining process objectives: Once the key processes have been identified, the next step is to define specific objectives for each process. These objectives should be aligned with the overall goals of the organization and should be measurable.
- Establishing process controls: The third step in the process approach is to establish controls for each process. These controls may include procedures, work instructions, quality standards, and performance indicators.
- Monitoring and measuring process performance: The process approach also involves monitoring and measuring the performance of each process. This may involve collecting data on key performance indicators and using that data to identify opportunities for improvement.
- Continuously improving processes: The final step in the process approach is to continuously improve processes based on the results of monitoring and measurement. This may involve making changes to procedures, updating work instructions, or introducing new technologies or tools.
Continual Improvement
Another notable and important aspect of ISO 9001 is its focus on continual improvement. This means that organizations are encouraged to continuously evaluate and improve their processes, products, and services to enhance customer satisfaction and achieve their business objectives. This improves performance and builds a better reputation with customers.
example of how it facilitates continual improvement is by management review. ISO 9001 requires top management to review the QMS regularly to ensure its continuing suitability, adequacy, and effectiveness. Management review includes reviewing performance data, evaluating the effectiveness of the QMS, and identifying areas for improvement. They also operate customer services where organizations are required to obtain customer feedback on their products and services to identify areas for improvement. This feedback can be used to drive improvements in processes, products, and services.
Customer Focus
ISO 9001 also highlights the significance of customer focus. Organizations are required to identify and understand their customers’ requirements and expectations, and to strive to meet or exceed those expectations through the consistent delivery of excellence within both products and services. Customers are the main priority.
Documentation and Record Keeping
Documentation and record-keeping are an essential part of ISO 9001, as they help to ensure that an organization’s Quality Management System (QMS) is effectively implemented, affirmed, and persistently improved. ISO 9001 requires organizations to establish and maintain a documented QMS that includes policies, procedures, work instructions, and other documents that describe how the organization operates its processes, controls its activities, and monitors its performance.
Certification
Organizations can seek certification to ISO 9001 by undergoing an independent audit of their QMS by a certification body. Certification can help organizations to demonstrate their commitment to quality and enhance their reputation with customers and other stakeholders.
To become certified, an organization must first establish and implement a QMS that meets the requirements of ISO 9001. The organization must then engage the services of an accredited certification body to conduct an audit of its QMS. The certification audit consists of two stages:
- Stage 1: The certification body reviews the organization’s QMS documentation to determine whether it meets the obligations of ISO 9001. This stage usually involves a review of the organization’s policies, procedures, and work instructions.
- Stage 2: The certification body performs an on-site audit to evaluate the execution and efficiency of the organization’s QMS. This stage involves interviewing employees, reviewing records, and observing processes to ensure that the QMS is being effectively implemented and that it meets the requirements of ISO 9001.
If the certification body determines that the organization’s QMS meets the requirements of ISO 9001, it will issue a certificate of conformity. The certification is typically valid for a period of three years, during which time the organization must undergo surveillance audits to maintain its certification, so the quality is always up to standard and that organizations are making the most of ISO 9001.
In conclusion, ISO 9001 provides a framework for organizations to implement a QMS and improve the effectiveness of their quality management processes. By adopting a process approach, focusing on continual improvement, prioritizing customer satisfaction, maintaining documentation and records, and seeking certification, organizations can enhance their quality management practices and better meet the needs of their customers.